The copyright of this article belongs to Siansonic Technology.The production is prohibited without permission.
Semiconductors are widely used in core industries such as computers, consumer electronics, telecommunications, and automotive electronics. The manufacturing process of each semiconductor product involves hundreds of steps, generally divided into eight stages: wafer processing, oxidation, photolithography, etching, thin film deposition, interconnection, testing, and packaging. The focus of our discussion today is photoresist, an essential semiconductor material used extensively in the manufacturing process of electronic components. It can be found in chips, panels, PCBs, photovoltaics, and integrated circuit packaging, among others. The production of a single chip requires 10 to 50 photolithography processes. Not only does the photolithography process require specific photoresist properties, but the photoresist coating process is also one of the critical factors.
Photoresist is a light-sensitive chemical substance consisting of three main components: photosensitive resin, sensitizer, and solvent. After exposure to light, the resist undergoes a chemical reaction, resulting in a change in solubility. By utilizing this property, specific patterns can be achieved on a substrate using a mask with a particular design. First, the photoresist is coated onto the semiconductor material. After exposure and development, the remaining photoresist serves as a protective layer for the underlying material. The etching process is then performed with an etching agent, ultimately transferring the precise patterns from the mask onto the substrate. As such, photoresist is a key material in microfabrication technology.
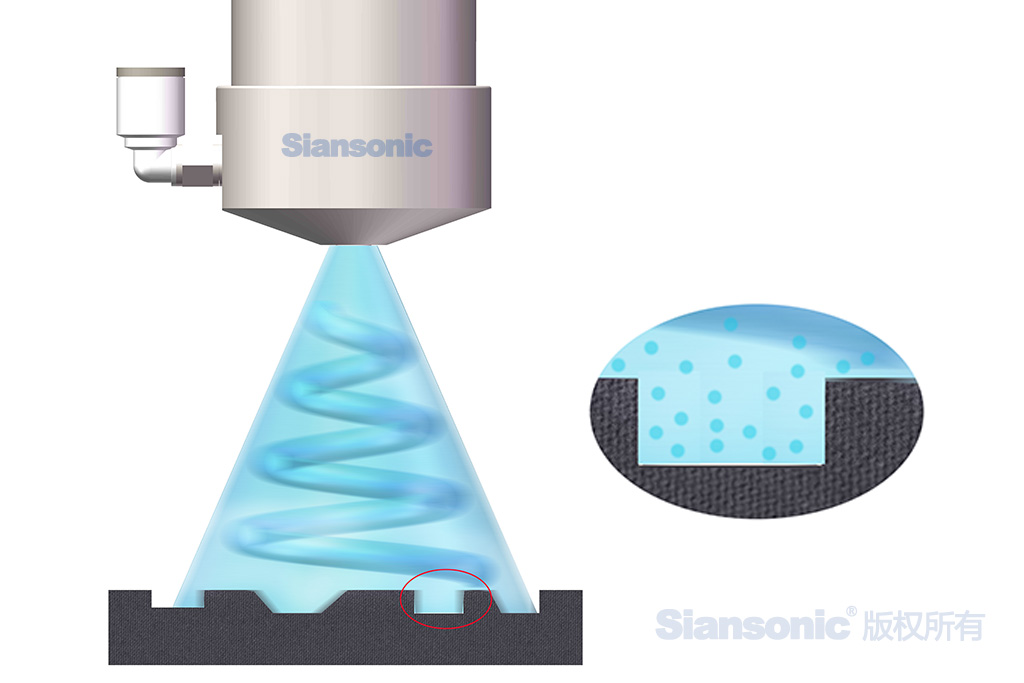
Figure 1. The ultrasonic photoresist coatings demonstration
Achieving an even and process-compliant photoresist spray coating onto the substrate surface is a critical challenge. Current photoresist spray coating techniques include spin coating, dip coating, and ultrasonic spray coating. Spin photoresist spray coating, also known as centrifugal rotation, involves dropping a specific amount of photoresist solution onto the substrate surface and then using centrifugal force to spread the resist across the substrate. This method can produce uniform photoresist films but often results in thinner films with unstable thickness adjustments. Moreover, excess photoresist is thrown off the substrate during the spin coating process, leading to waste. Dip photoresist spray coating, while offering high efficiency and better utilization of the coating material, is only suitable for simple, streamlined materials and can be difficult to control in terms of coating volume.
Ultrasonic photoresist spray coating uses high-precision syringe pumps to accurately control the flow of photoresist, atomizing and dispersing the resist as it passes through the ultrasonic nozzle. Pressurized airflow then directs the atomized resist directly onto the substrate surface, forming a controllable photoresist film thickness without the need for rotation. This method is not limited by the substrate's coating area and offers an easily controlled and adjustable process, effectively ensuring product quality stability and minimizing photoresist waste.
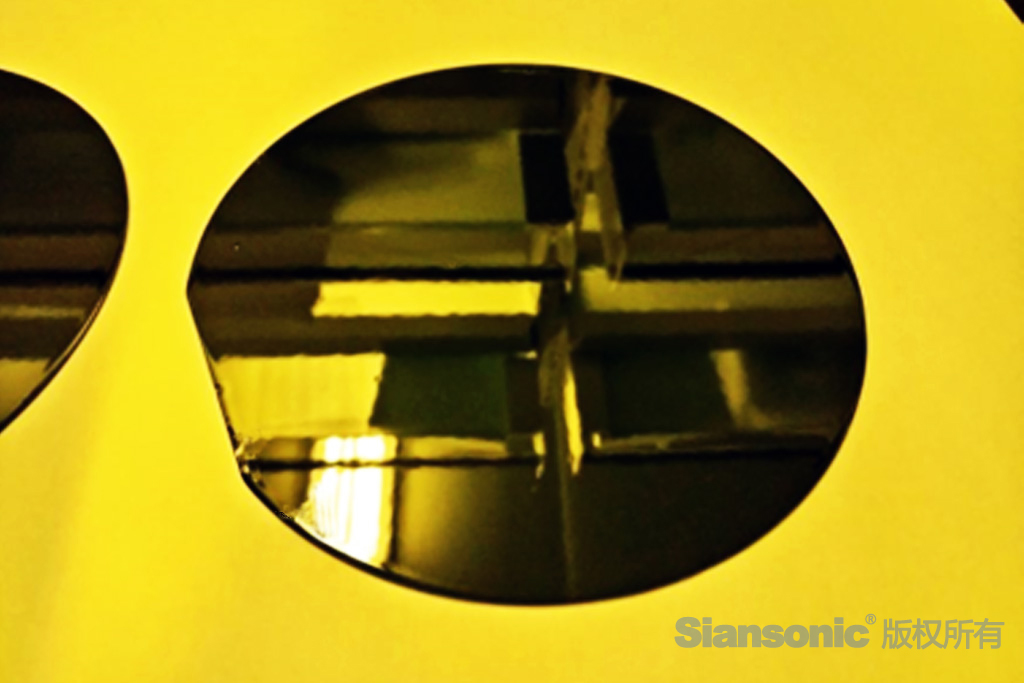
Figure 2. The photoresist coating on wafer
Siansonic Technology is specializing in ultrasonic spray coating technology, providing professional equipment and solutions for various thin-film coatings, especially in photoresist spray coating applications. With over 30 years of industry experience, Siansonic 's ultrasonic spray coating systems contribute to the semiconductor photoresist spray coating field, using ultrasonic technology to power the future.