The copyright of this article belongs to Siansonic Technology.The production is prohibited without permission.
Shower type megasonic cleaning nozzle is based on a method of cleaning that operates through spray nozzles aimed at the object to be cleaned. The mechanism behind is it involves embedding a megasonic transducer into the nozzle, enabling the flowing water to transmit megasonic wave energy to the surface of the object being cleaned, thus achieving the purpose of cleaning. One of the main advantages of shower type megasonic cleaning nozzle is its direct, point-to-point interaction with the surface of the object, allowing the sonic energy focus to make direct contact with the surface. In comparison to the batch type megasonic cleaning system, the megasonic conversion efficiency of the shower type megasonic cleaning nozzle is higher, and it also avoids the problem of uneven sonic field intensity due to different liquid depths. Additionally, as the shower type megasonic cleaning nozzle uses flowing liquid, it prevents the issue of residual dirt causing secondary contamination of the cleaned object.
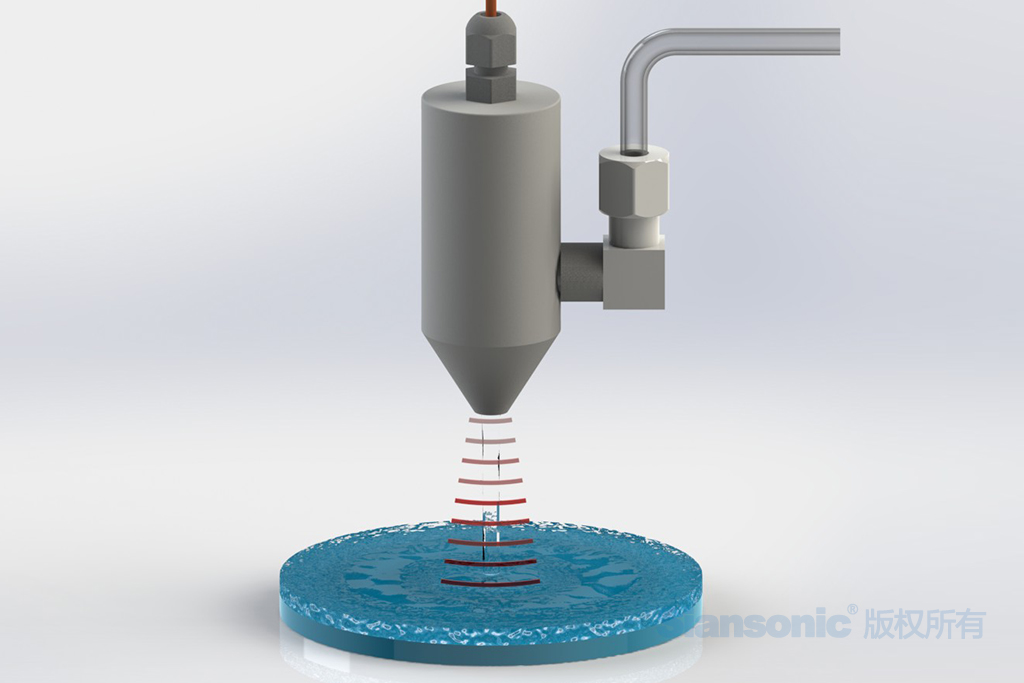
Figure 1. The schematic diagram of megaosnic cleaning nozzle
In terms of bulk semiconductor wafer cleaning, batch type megasonic cleaning system is undoubtedly the more efficient choice. Therefore, to save costs and increase efficiency, batch type megasonic cleaning system is usually the preferred method in the 90-65nm processes. However, for batch type megasonic cleaning system, there is a higher risk of cross-contamination. In processes with even lower linewidths, where the tolerance for impurities is lower, the use of single wafer cleaning technology becomes more prevalent. In order to avoid the high costs associated with repeated cleaning and reduce the rate of defective products, minimizing waste is a crucial strategy in wafer production. In a chip manufacturing process, the cleaning operation is repeated multiple times, with cleaning steps accounting for over 30% of the entire manufacturing process. As production progresses, both the number and importance of cleaning operations increase. To ensure product quality, almost every step of the process requires cleaning. It is estimated that for a DRAM factory producing 100,000 wafers per month, a 1% increase in yield can increase annual profits by $30 to $50 million for customers.
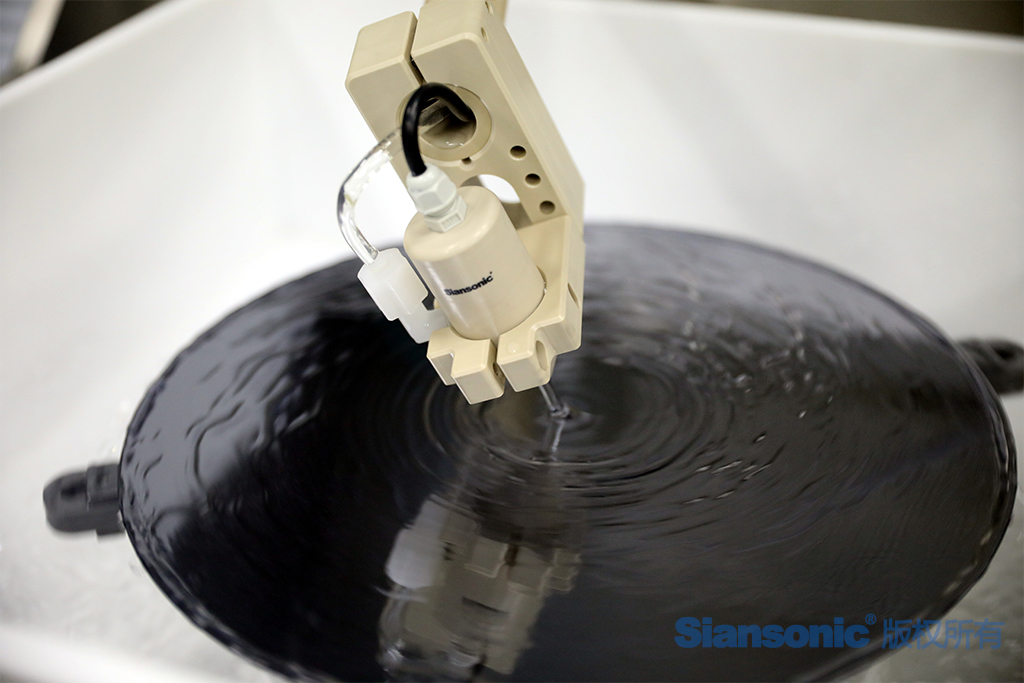
Figure 2. The shower type megasonic cleaning nozzle by Siansonic Technology
The shower type megasonic cleaning nozzle can be combined with motion components to achieve cleaning across an entire two-dimensional plane. It's suitable for cleaning various flat substrates, including semiconductor wafers. Siansonic's shower- type megasonic cleaning nozzle are made entirely of non-metallic, corrosion-resistant materials, capable of withstanding a variety of acids, bases, and organic solvents. Additionally, the use of a unique transducer attachment technique ensures higher stability and durability. Siansonic Technology offers various types of megasonic cleaning systems and comprehensive solutions for applications in diverse fields.