The copyright of this article belongs to Siansonic Technology.The production is prohibited without permission.
TCO glass is a type of conductive glass primarily used in fields such as transparent conductive electrodes and high-temperature electronic devices, including solar cells, liquid crystal displays, photodetectors, and window coatings. Its full name is Transparent Conductive Oxide Coated Glass, which involves uniformly coating a layer of transparent conductive oxide film on the surface of flat glass through physical or chemical deposition methods. The film mainly consists of oxides of indium (In), tin (Sn), zinc (Zn), and cadmium (Cd), as well as their composite multi-element oxide film materials. TCO glass is typically classified based on different film materials, such as Indium Tin Oxide (ITO), Aluminum-doped Zinc Oxide (AZO), Zinc Oxide (ZnO), and Fluorine-doped Oxides.
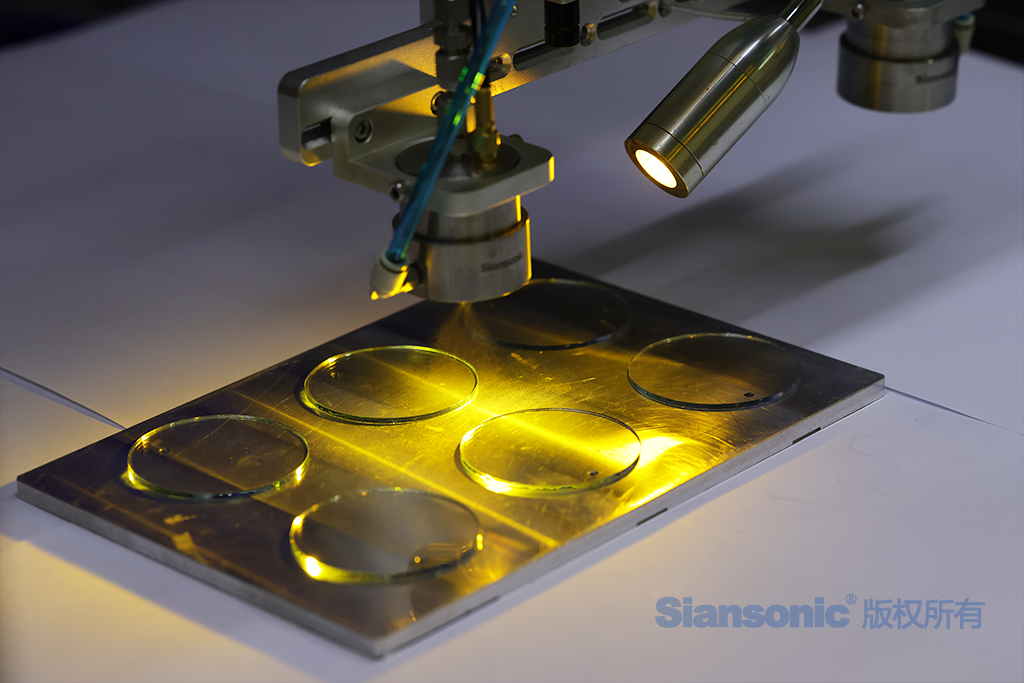
Figure 1.Preparation of TCO glass layer by ultrasonic spray pyrolysis
In the photovoltaic cell application field, the performance requirements for TCO glass mainly focus on spectral transmittance, electrical conductivity, and haze. The importance of electrical conductivity is self-evident. TCO glass needs to ensure a relatively high spectral transmittance to fully absorb and utilize sunlight, while a certain level of haze is required to enhance the light absorption capability of the semiconductor layer in thin-film cells, which refers to the scattering ability of transmitted light. Unlike ordinary glass, which requires a smoother surface, the photovoltaic industry may require TCO glass surfaces with particles of 100-500 nm in diameter to achieve the desired haze level.
The ultrasonic spray pyrolysis is a technique for preparing transparent conductive oxide (TCO) nano-thin films using ultrasonic spray pyrolysis. During the ultrasonic spray pyrolysis process, the precursor solution is uniformly atomized into micron-sized liquid particles by an ultrasonic spray nozzle and then deposited onto a heated substrate. For example, the precursor solution of aluminum zinc oxide is sprayed onto a substrate at approximately 300-500 degrees Celsius. During the coating process, the solvent evaporates, and the solute undergoes rapid thermal decomposition upon contact with the high-temperature substrate, resulting in the growth of a ZnO crystal film on the substrate surface. The temperature of the substrate typically plays a crucial role in determining the morphology of the film.
The ultrasonic spray pyrolysis is a more cost-effective and efficient coating that serves as an alternative to vacuum deposition and sputtering. The droplet size produced by the ultrasonic spray nozzle is highly uniform and controllable, allowing all droplets to react simultaneously in the same manner during deposition, providing a more efficient TCO production process in both research and large-scale production. The ultrasonic spray pyrolysis for depositing TCO transparent conductive oxide nano-thin films is a nano-thin film preparation technology with broad application prospects.