The copyright of this article belongs to Siansonic Technology.The production is prohibited without permission.
Ultrasonic spraying is a technique known for its uniformity, high slurry utilization, and controllable spraying thickness. The ultrasonic atomization nozzle is its key component. Ultrasonic atomization nozzle works by converting high-frequency sound waves into mechanical energy. This energy creates standing waves in liquids, breaking them into uniformly tiny droplets as they leave the nozzle's atomizing surface. Typically, these atomized droplets are micron-sized. To accommodate various applications, ultrasonic atomization nozzles come in different models.
The K series ultrasonic atomization nozzle, a kind of ultrasonic atomization nozzle with wide spray, known as the K series ultrasonic atomization nozzle, is suitable for large-area spraying tasks. Ultrasonic atomization nozzle employs ultrasonic atomization technology, where the spray, carried by a controlled stream through a flattened air guide plate, forms a fan-shaped mist that eventually coats the substrate in an elliptical shape. By combining multiple ultrasonic nozzles in parallel, a wider spray width can be achieved, making it ideal for mass production spraying processes. Theoretically, linking multiple ultrasonic nozzles can achieve limitless spraying widths. When spraying areas exceed 200*200mm, efficiency becomes significantly more important, making the widemist ultrasonic atomization nozzle a preferred choice even in experimental spraying stages.
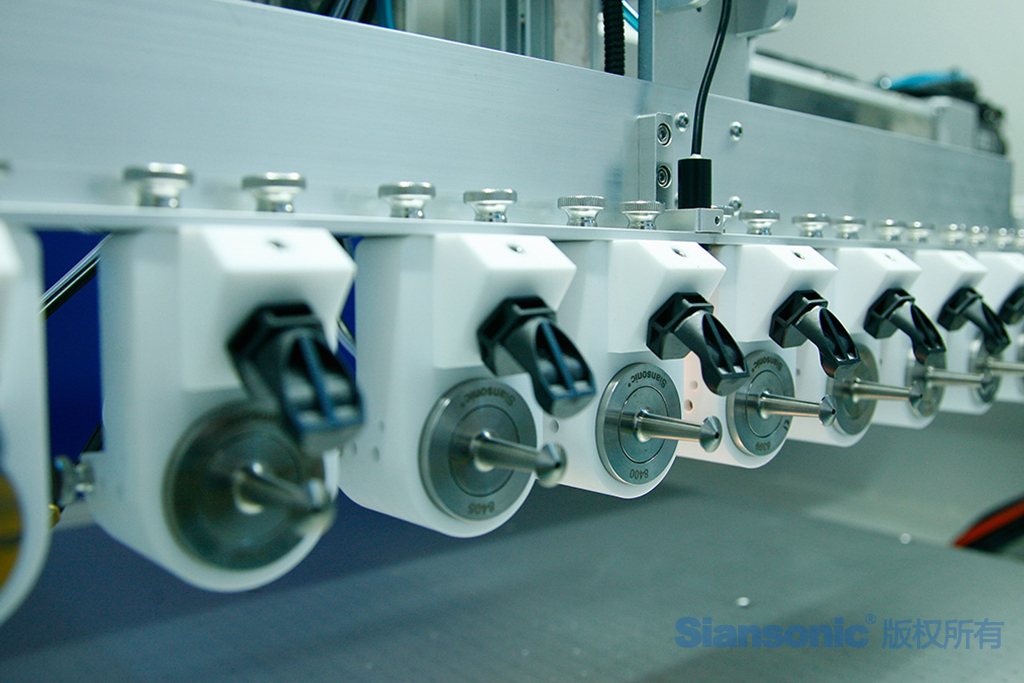
Figure 1. The K series ultrasonic nozzle array
The single nozzle of the widemist ultrasonic atomization nozzle can cover a spray width of 40-150mm, achieving a material utilization rate of over 85%, four times that of traditional two-fluid spraying. It offers high uniformity and precise control over spraying thickness. Theoretically, aligning 30 widemist ultrasonic atomization nozzles in parallel can cover a spray width of 3-4 meters. Arrays of ultrasonic atomization nozzles can be used for large area spraying processes, such as spraying catalysts on fuel cell membrane electrodes, applying anti-reflective films for augmented reality, spraying thermal insulation films, applying superhydrophobic sprayings, and soldering flux spraying.