The copyright of this article belongs to Siansonic Technology.The production is prohibited without permission.
Ultrasonic spray coating, a breakthrough in industrial and research applications, is increasingly supplanting traditional coating methods because it is precision, control, repeatability, and eco-friendliness stand out. At its core is the ultrasonic spray nozzle. Leveraging the Langevin transducer principle, this ultrasonic spray nozzle converts high-frequency sound waves into mechanical energy. This energy is transferred to liquids, generating standing waves. As the liquid exits the ultrasonic spray nozzle, it breaks into micro-sized, uniform droplets. These droplets are then precisely guided onto the substrate using an extremely low guiding carrier gas, creating an even coating or film. Thus, the essence of ultrasonic spray coating is captured.
Unlike air nozzles, ultrasonic spray nozzles don't require small openings for atomization. They employ larger apertures to atomize liquids without pressure, utilizing ultrasonic vibrations. This design not only avoids nozzle clogging but also produces low-speed sprays that are more controllable and virtually eliminate splashing. Each ultrasonic spray nozzle works at a specific resonant frequency, which dictates the atomized particle size. By choosing ultrasonic spray nozzles of different frequencies, diverse spray coating needs are met. For instance, a 120KHz ultrasonic spray nozzle, when tested with water, it generates an average droplet size of 15um. Higher frequencies results in smaller particle sizes. Ultrasonic spray nozzles come in various types based on spray range: WideMist ultrasonic spray nozzle, FocusMist ultrasonic spray nozzle, NanoMist ultrasonic spray nozzle, and LineMist ultrasonic spray nozzle. Additionally, for unique applications, specialized ultrasonic spray nozzles like ConeMist ultrasonic spray nozzle, Penetrator ultrasonic spray nozzle, Pyrolysis ultrasonic spray nozzle, and drying ultrasonic spray nozzle have been developed. The Pyrolysis and drying ultrasonic spray nozzles are specifically designed for ultrasonic spray pyrolysis and ultrasonic drying processes in ultra-fine powder production.
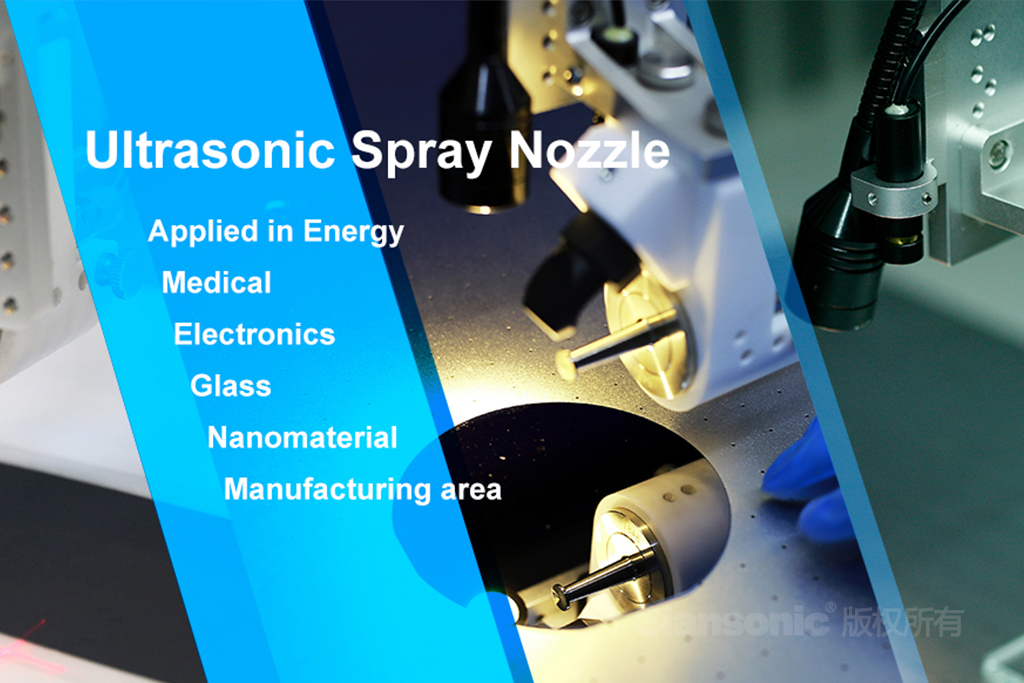
Figure 1. different ultrasonic nozzle
Earlier, we discussed the spray produced by ultrasonic spray nozzles is low-speed and gentle. To guide this mist, a bit of carrier gas is needed. Thus, besides the ultrasonic generator, these ultrasonic spray nozzles also include an air shaping device. The air shaping device determines the spray shape – whether it's a wide, flat fan, a cone, or a fine linear pattern.
WideMist ultrasonic spray nozzle: The spray, carried by controlled air through a flat guide plate, forms a fan shape, hitting the substrate in an elliptical pattern. By adjusting the spray height, the width of the spray on the substrate can be modified. Using multiple widemist ultrasonic spray nozzles in parallel allows for wide-area applications.
FocusMist ultrasonic spray nozzle: Features a specialized constrictive channel design for evenly focused distribution of carrier gas. The spray is focused by the carrier gas, effectively reducing the spray coating area. Ideal for smaller area applications.
NanoMist ultrasonic spray nozzle: Generates highly focused spray via an external liquid feed, offering smaller spray areas and more precise flow control. Typically used for drug-eluting stent coatings, especially for small stents like coronary and intracranial stents. The external liquid feed greatly reduces issues like polymer solution agglomeration caused by ultrasonic effects.
LineMist ultrasonic spray nozzle: This type offers the narrowest spray width among ultrasonic spray nozzles. Through unique liquid and gas channel designs, it creates the finest and clearest lines. It is ideal for various small-area or linear spray coating applications.
ConeMist ultrasonic spray nozzle, also known as the swirl spray ultrasonic spray nozzle: It employs a special vortex channel design, transforming the carrier gas into a uniform swirling airflow. This results in a cyclone-like dispersal of the spray, enhancing coating effectiveness on vertical or curved substrates with angles.
Penetrator ultrasonic spray nozzle, as the name suggests, penetrates the substrate for spraying: This extended version of the ultrasonic spray nozzle features a lengthened front end for spraying in narrow spaces. It’s primarily used for applications like coating the inner walls of vacuum blood collection tubes, silicone oil spraying inside syringes, and other tubular interiors.
Siansonic Technology with nearly 40 years of dedication to ultrasonic and piezoelectric technologies, is committed to providing professional and high-quality ultrasonic spray nozzle products and one-stop ultrasonic spray coating solutions to a wide range of customers and markets.