The copyright of this article belongs to Siansonic Technology.The production is prohibited without permission.
During the manufacturing process of semiconductor devices, various cleaning methods have been developed, including laser-induced shockwave cleaning, liquid carbon dioxide cleaning (snow cleaning), wet cleaning, and megasonic clean, which are used to remove particles from the surface of silicon wafers. However, as particle sizes decrease, the cleaning process becomes more difficult, regardless of the method used. This is because, as particle sizes decrease, the distance between the particles and the substrate also reduces, leading to an increase in adhesion forces, which significantly affects particle removal efficiency. Therefore, chemical methods are typically employed to remove nanoparticles. However, chemical methods can cause excessive material loss, making them an unsuitable choice for semiconductor processes. As a result, physical force-based cleaning methods, such as megasonic clean, are a better option.
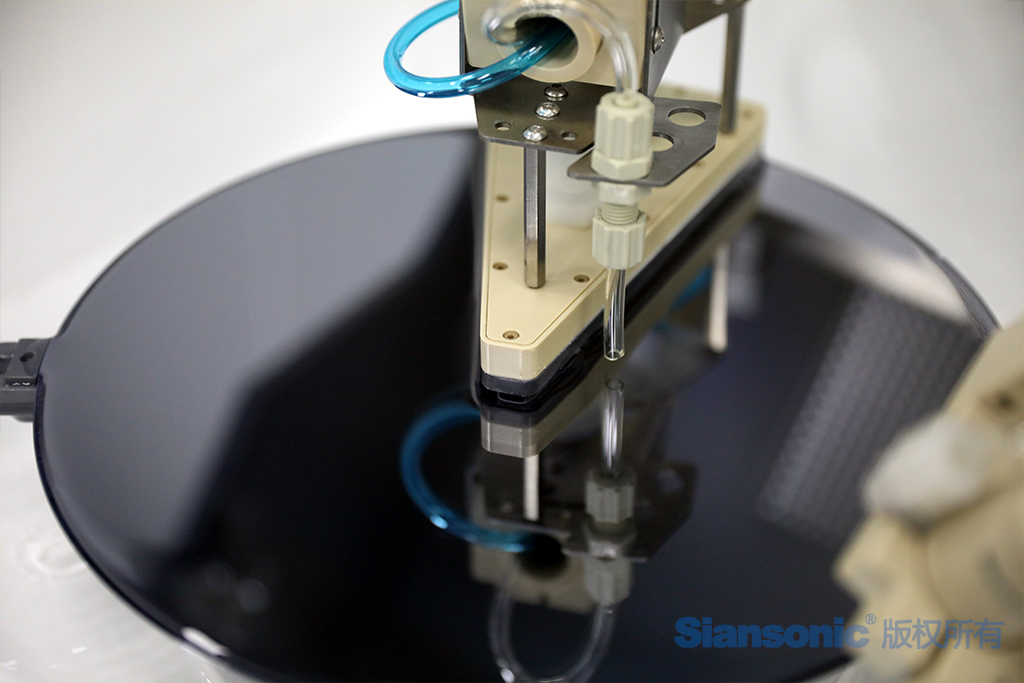
Figure 1. Megasonic clean equipment for wafer cleaning
When cleaning nanoparticles in delicate nanoscale patterned structures, any form of physical contact can cause damage to the structures. Megasonic clean is a non-contact cleaning process that can remove particles, including those in grooves. However, during the megasonic clean process, strong physical forces such as cavitation are generated, so it is crucial to control the damage to the patterns. Various parameters, including megasonic power, frequency, and ultrasonic pulses, can affect the cavitation phenomenon, influencing the characteristics and size of cavitation bubbles. Both low-frequency and high-frequency ultrasound generate cavitation phenomena, with bubbles oscillating either in a stable or transient manner. For example, the difference caused by ultrasound frequency is in the size of bubbles at resonance. Cavitation bubbles produced by megasonic waves are micron-sized, while those generated by low-frequency ultrasound are sub-millimeter-sized. If non-uniform bubble nuclei of sub-millimeter size are present in the water, low-frequency ultrasound can more easily trigger cavitation bubble nuclei. In cases of transient cavitation, the violent collapse of bubbles can cause damage to the surface of the cleaned object. When using higher frequency ultrasound, the size of cavitation bubbles decreases, allowing for more stable oscillations, which in turn reduces erosion on the surface of the object being cleaned. For cleaning silicon wafers, megasonic clean with smaller cavitation erosion is clearly a better choice. Naturally, these parameters also affect particle removal efficiency.
The adhesion forces that megasonic clean needs to overcome are primarily Van der Waals forces, electrostatic forces, and covalent bonds between the surface of the object being cleaned and the contaminants. The cleaning process driven by acoustic cavitation determines the performance of megasonic clean, which can be achieved by controlling bubble dynamics to induce stable and transient cavitation. Stable cavitation can generate particle removal forces, whereas transient cavitation results in destructive forces. Compared to increasing the number of bubbles near the object being cleaned by adjusting physical parameters such as reducing frequency to improve cleaning efficiency, modifying the chemical environment is a more desirable approach, as adding certain chemical components can stabilize bubbles and maintain the required frequency. Additionally, optimizing the chemical environment is easier than optimizing the physical parameters of the megasonic clean system. For instance, adding dissolved gases can greatly increase cavitation intensity. To reduce this heightened cavitation, surfactants can be used to mitigate it, although this may also lower surface tension, thereby improving acoustic streaming. However, compared to the cavitation effect, this influence is less significant.
In the actual semiconductor industry, contamination levels are very low, yet removing such contamination from fine patterns remains challenging. Researchers have studied the chemically controlled megasonic clean mechanism and found that adding hydrogen to deionized water can improve particle removal efficiency, but it also leads to more severe pattern damage. To minimize pattern damage, researchers added anionic surfactants to deionized water and discovered that with a very low addition of surfactants, particle removal efficiency improved. However, when the surfactant concentration increased (100 ppm), the particle removal efficiency dropped sharply to zero. In contrast, pattern damage continuously decreased as surfactant concentration increased. High-speed camera results confirmed that at a surfactant concentration of 20 ppm, there was a larger population of bubbles. However, at 100 ppm, the bubble population became negligible, as the bubble nuclei were covered by the surfactant and behaved like solid particles. When performing megasonic clean in deionized water with hydrogen, due to the high growth rate and agglomeration of bubbles, both particle removal efficiency and pattern damage were observed to be higher. This indicates that microstreaming, the quantity of bubbles, and bubble aggregation play a crucial role in determining the efficiency of particle removal from silicon wafer surfaces and the extent of pattern damage during megasonic clean. Therefore, in semiconductor cleaning processes that use megasonic clean, it is essential to find the right frequency and power parameters, while also carefully controlling the number of bubbles in the cleaning liquid.
Siansonic provides various types of megasonic clean systems for fields such as CMP (Chemical Mechanical Polishing), pre-bonding cleaning, mask cleaning, developing, photoresist removal, metal stripping, and wet etching. These include bonded megasonic clean systems, spray megasonic clean nozzles, and tank megasonic clean equipment.