The copyright of this article belongs to Siansonic Technology.The production is prohibited without permission.
Lithium-ion batteries, utilized in everyday devices like mobile phones and laptops, boast a high energy density. They provide significant power output, making them suitable for numerous portable devices. Additionally, these batteries offer the advantages of rapid charging, long cycle life, safety, and environmental friendliness.
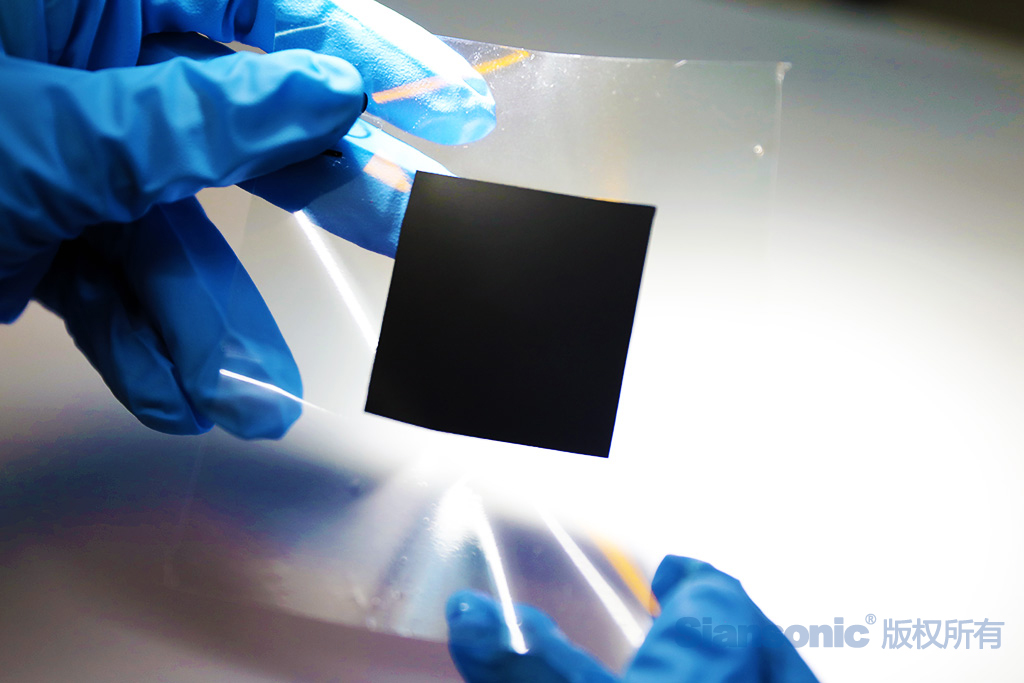
Figure 1. The membrane electrode prepared by ultrasonic spray coating technology
Lithium-ion batteries function by the movement of lithium ions between the anode and cathode, with charging and discharging essentially being the insertion and extraction of these ions. Comprising electrodes (anode and cathode), electrolyte, and a separator, these batteries work as follows: during charging, external circuits drive lithium ions into the anode while ions detach from the cathode into the electrolyte, storing electrical energy as chemical energy. During discharge, ions move from the anode into the electrolyte and then into the cathode, converting stored chemical energy back into electrical energy. The separator, a porous polymer membrane between the anode and cathode, prevents self-discharge and short-circuiting by keeping the electrodes apart. It's noteworthy that traditional anode materials face challenges like slow kinetics, significant volume expansion, and unstable interfaces during charge/discharge cycles, posing considerable hurdles for lithium-ion battery development. Coating strategies effectively address these issues, enhancing electrochemical performance and endowing anode materials with superior ionic/electronic conductivity, elasticity, and an inert interface layer, thus ensuring stability and continuity in lithium-ion battery systems.
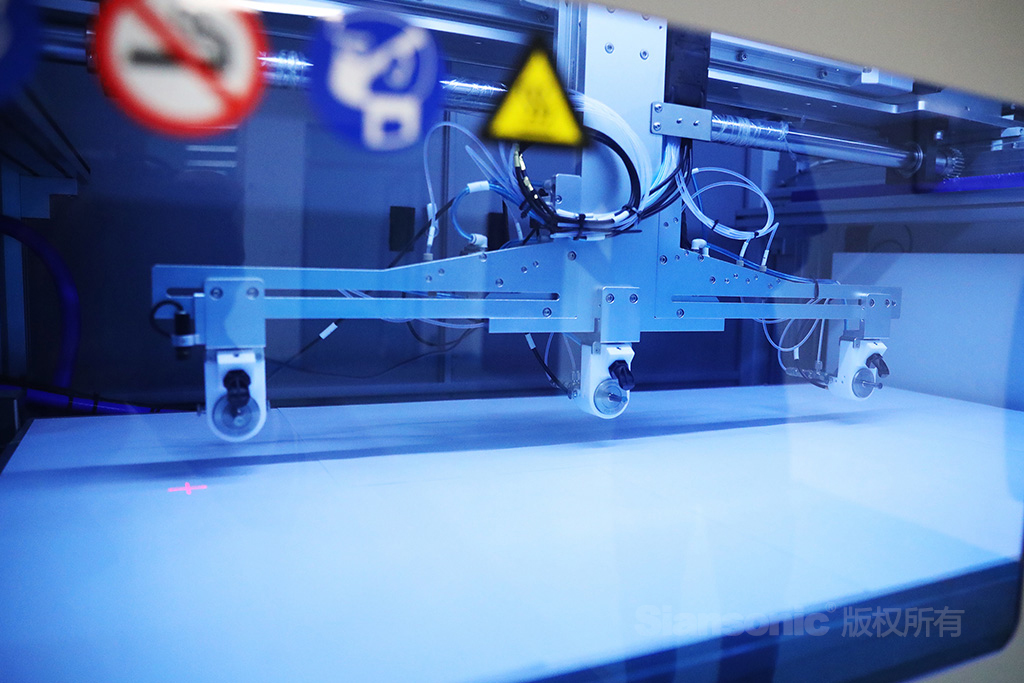
Figure 2.The ultrasonic spray nozzle used for prepare large area of catalyst coating
Ultrasonic spray coating system opens new possibilities for applying coatings to lithium battery electrode materials. Ultrasonic spray coating’s core, ultrasonic atomization, turns liquid materials into uniformly sized particles via varying frequencies, depositing them onto substrates. This process ensures controllable particle size and even distribution, greatly enhancing coating uniformity. Ultrasonic spray coating allows for precise flow control, effectively managing coating thickness. Moreover, Ultrasonic spray coating boasts high material utilization, precise thickness control, thinner coatings, minimal splashing, non-clogging nozzles, and low maintenance costs. Ultrasonic spray coating has found widespread applications in new energy, biomedical, and semiconductor industries.