The copyright of this article belongs to Siansonic Technology.The production is prohibited without permission.
A safe, environmentally friendly and reliable energy supply is essential for sustainable human development and a high quality of life, and hydrogen is a recognized clean energy source. When hydrogen is electrochemically oxidized in a fuel cell system, the only by-product is pure water with no carbon dioxide emissions.
Hydrogen is the most abundant chemical element in the universe, making up 75% of the normal mass of matter, which is a rich source of energy. It is clear that hydrogen energy and fuel cells can meet the growing needs of social development and have the potential to cover most energy sectors. Fuel cell is a kind of energy conversion device, as long as the fuel and oxidizer are available can continuously convert the chemical energy in the fuel cell into electric energy, compared with the traditional combustion technology, the fuel cell does not go through the combustion process, so it is not subject to the limitations of the Carnot cycle, and the efficiency of the energy conversion can reach 60% or higher.
There are many types of fuel cells, but they all usually work in the same way. Essentially, a fuel cell consists of three adjacent parts, anode, electrolyte, and cathode. Based on the type of electrolyte, fuel cells are categorized as alkaline fuel cells (AFC), proton exchange membrane fuel cells (PEMFC), phosphoric acid fuel cells (PAFC), molten carbonate fuel cells (MCFC), and solid oxide fuel cells (SOFC). Among them, PEMFC stands out among all types of fuel cells with unique advantages such as fast start-up time, wide range of operating temperatures, and high specific energy, and is widely used in fuel cell vehicles and stationary applications.
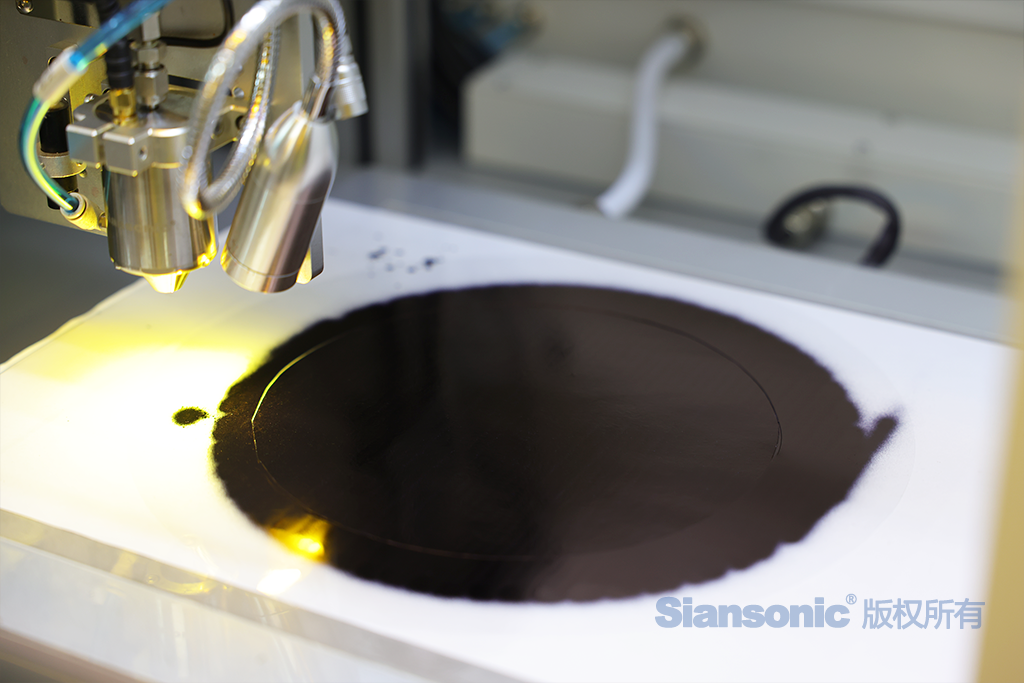
Figure 1.Ultrasonic nozzle spray catalyst in membrane electrode
The core component of a PEMFC is the MEA, or membrane electrode, which is a component that includes a membrane, a gas diffusion layer, and a catalyst layer to provide micro-channels for mass transfer and electrochemical reactions, and is a major part of the PEMFC that affects its performance, durability, and cost. One of the problems faced during the production of membrane electrodes is the coating of the catalyst. The advantages of ultrasonic catalyst coating technology in catalyst coating have been discovered through the efforts of researchers. ultrasonic catalyst coating is a combination of spraying and ultrasonic atomization, in which the catalyst slurry is dispersed by ultrasonic waves into tiny droplets and then deposited and coated onto the gas diffusion layer as well as the proton-exchange membrane, which will have two catalysts, one of which is the catalyst. The membrane electrodes formed by pressing the gas diffusion layer and proton exchange membrane with two catalyst coating layers show better performance with low resistance, good proton transfer capability, high Pt utilization and low cost.
As a coating process with the advantages of high coating uniformity, high raw material utilization, high precision of coating thickness control, thinner coating thickness, less spattering, nozzle non-clogging, and low maintenance cost, ultrasonic catalyst coating system has been widely used in a variety of coating fields.