The copyright of this article belongs to Siansonic Technology.The production is prohibited without permission.
Spraying is a common process that involves adhering a material to the surface of a tool or device. Common types of spraying include air spraying, thermal spraying, and ultrasonic atomizing spraying. Each process has its characteristics and is suitable for different application areas.
Both ultrasonic spraying and air spraying disperse liquid slurry into fine droplets through a certain "force" and then coat the substrate surface. The "force" in ultrasonic spraying is ultrasonic waves, while in air spraying, it is gas pressure. Compared to air spraying, ultrasonic spraying does not require high air pressure, thus avoiding severe droplet splashing. Moreover, the atomization flow rate of ultrasonic spraying is highly controllable, allowing for spraying operations at very low supply flow rates. Therefore, ultrasonic spraying is suitable not only for large-scale applications but also for precise spraying on very small areas.
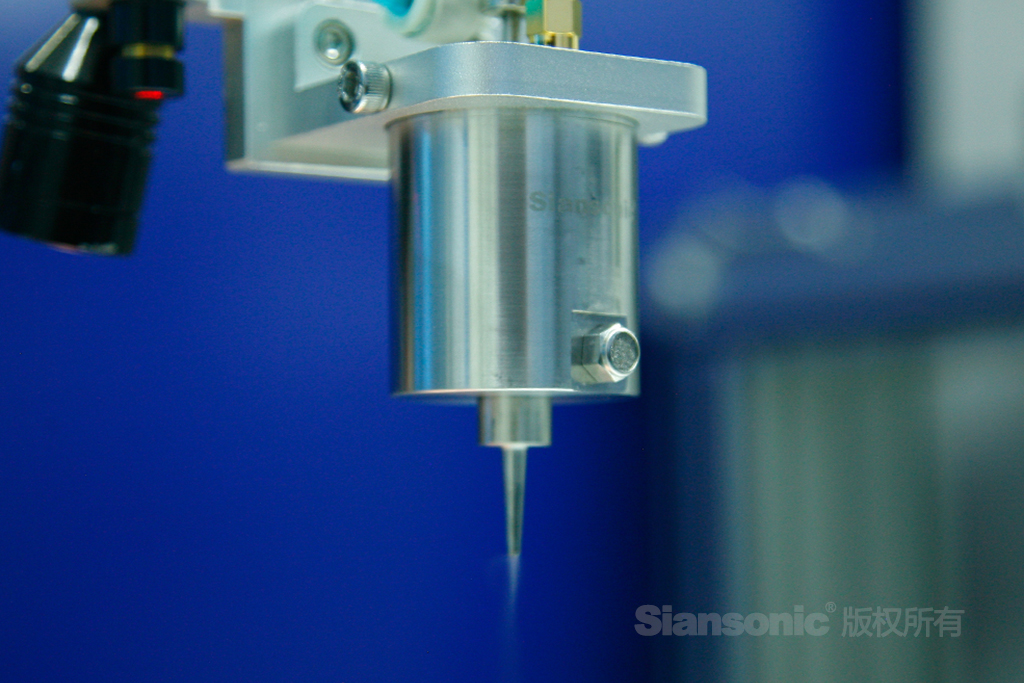
Figure 1. Siansonic's Linemist Ultrasonic Nozzle
One characteristic of ultrasonic spraying is the precise control over the spray area. Whether it's for larger substrates or detailed device surfaces, the flexibility is achieved with the linemist ultrasonic nozzle, which has an extremely narrow spray width ranging from 0.5 to 1 mm. Due to the unique design of the liquid and gas flow channels, the spray width of the linemist ultrasonic nozzle is unaffected by the height of the nozzle, making it a better choice for applications where spray width needs to be very fine but nozzle height adjustments are restricted. In the field of fine device spraying, the linemist ultrasonic nozzle can use lower flow rates to spray more precise and clear lines or areas.
Siansonic, with nearly 40 years of experience and technology in the piezoelectric and ultrasonic fields, provides suitable ultrasonic nozzles, ultrasonic spraying system, and complete solutions for various applications.